
The steel industry has long been the backbone of the American manufacturing landscape. From sky-piercing skyscrapers to the sleek frames of automobiles, steel's presence is seen and felt in nearly every corner of modern life. But who are the powerhouses behind this vital material's production?
Understanding the key players in the US steel market gives us not only an idea of where our steel comes from but also unveils the intricacies of production that these giants manage. By knowing these suppliers, we can appreciate the scale and sophistication of operations that keep the wheels of progress turning.
- Introduction to the US Steel Industry
- Profiles of Leading Steel Suppliers
- Market Dynamics and Supply Chain
- Technological Innovations in Steel Manufacturing
- Future Outlook for the Steel Industry
Introduction to the US Steel Industry
The United States has long been a titan in the global steel industry, a proud symbol of industrial strength and manufacturing prowess. With roots stretching back to the 19th century, the history of American steel is closely tied to the growth of its railroads, the expansion of its cities, and the development of its military power. In today's world, steel production remains a cornerstone of American infrastructure, supporting everything from construction and transportation to renewable energy systems. Although the industry has faced its fair share of challenges, from environmental concerns to foreign competition, it continues to adapt and innovate, ensuring its place at the heart of the nation's economy.
Modern steel manufacturing facilities in the US embrace a combination of traditional techniques and cutting-edge technologies to produce millions of metric tons of steel annually. Historically, cities like Pittsburgh became synonymous with steel, yet the industry has since expanded across multiple regions, boasting highly efficient plants and thousands of skilled workers. This transformation was propelled by the industry's commitment to reducing emissions, optimizing energy use, and enhancing production quality, ensuring that American steel manufacturing remains competitive on a global scale.
Steel suppliers are now embracing new dynamics, including the rise of mini-mills and a focus on recycling. The electric arc furnace (EAF) method, which relies heavily on recycled scrap metal, has gained traction for its lower environmental impact and cost-effectiveness compared to traditional furnaces. This shift not only signifies a greener approach but also highlights the industry's responsiveness to shifting economic and environmental imperatives. As the steel industry evolves, so too do the needs and demands of its diverse clientele, ranging from massive construction projects to delicate high-tech applications.
"The story of American steel is the story of America itself. As it goes, so too does our nation's industrial might." – Anonymous Industry Expert
Amid the ups and downs, the industry has consistently demonstrated resilience and versatility. Recent data indicate that the US ranks among the top global steel producers, with its suppliers catering to both domestic and international markets. An intriguing facet of this ecosystem is its supply chain's complexity, involving intricate logistics and strategic partnerships with both raw material providers and end-users. This holistic approach allows for seamless operations that meet the demands of various sectors, including automotive, construction, and energy.
The American steel industry signifies more than just raw output; it's also about innovation and the relentless pursuit of excellence. The sector includes longstanding industry giants that have backed decades of economic growth, alongside nimble newcomers who bring fresh perspectives and advanced techniques. This blend of the old and new strengthens the industry's foundations, ensuring that future challenges will be met with enthusiasm and ingenuity. As new demands emerge and technologies advance, the US steel industry stands poised to continue as a leader, pushing boundaries and setting benchmarks for the world to follow.
Profiles of Leading Steel Suppliers
In the thriving world of American steel, a few key players dominate the skyline, shaping the landscape of industry and innovation. At the forefront is Nucor Corporation, renowned as one of the largest producers of steel and steel products in North America. Nucor is unique for its ability to innovate and adapt, having spearheaded the electric arc furnace method, which revolutionized cost-efficiency in steel production. Their fiercely independent ethos allows them to maintain flexibility in operations, providing a broad range of steel products that cater to diverse market needs. As one of the industry's leaders, Nucor’s impact is palpable across various infrastructure projects, providing a testament to their significant footprint in the world of steel manufacturing.
No discussion about steel in the US can overlook U.S. Steel, a storied company that has played a pivotal role in the country's industrial development. Founded in 1901, U.S. Steel has a rich heritage that blends tradition with modern necessities. They are recognized for producing high-quality flat-rolled and tubular products. Their commitment to sustainability is noteworthy, as the company endeavors to reduce its carbon footprint by investing in renewable energy and cutting-edge technologies that promise cleaner steel production. This dedication not only garners respect but also sets a benchmark for responsibility in the sector.
Another titan, Steel Dynamics Inc., emerges as a versatile player that continues to expand its influence. Known for producing a wide array of steel products, they maintain a competitive edge through highly efficient operations and an integrated approach that encompasses both recycling and production. Their robust network of operations across North America enables rapid distribution and enhanced customer engagement. An insightful report by the World Steel Association highlighted Steel Dynamics for their notable contributions to the industry's growth trajectory, a sentiment echoed by stakeholders who rely on their consistent output.
Beyond these giants, other significant contributors add to the fabric of the US steel industry. Companies like ArcelorMittal, notable for their technical expertise and innovation, contribute variety and competitiveness to the market. Their dedication to advanced research and development ensures a steady stream of innovative products that meet the ever-changing demands of modern engineering and architectural endeavors. Collectively, these suppliers sustain a vibrant ecosystem that fuels economic growth, provides employment, and supports countless sectors with crucial resources.
“The American steel industry has always been a tapestry of resilience and ingenuity. By continuously overcoming challenges, these leading suppliers not only meet market demands but also drive progress within and beyond the industry,” said an industry expert from the American Iron and Steel Institute.
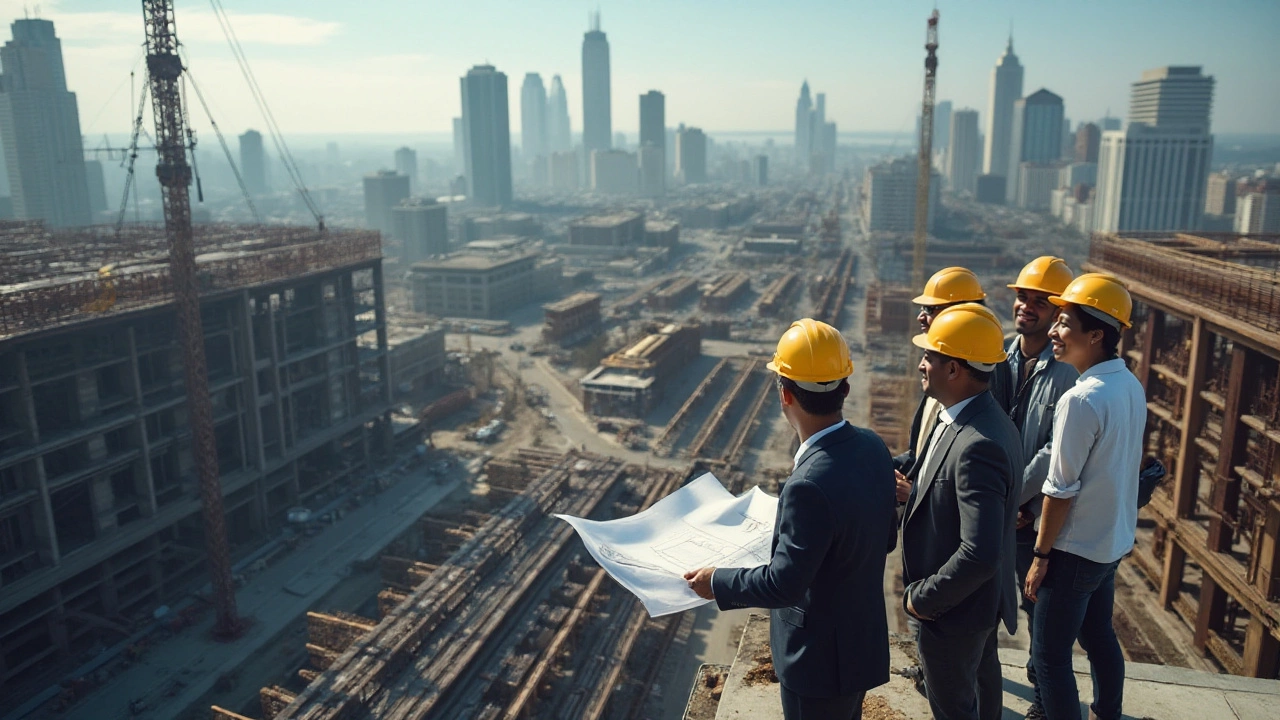
Market Dynamics and Supply Chain
The landscape of the US steel industry is heavily influenced by a complex web of market dynamics and supply chain intricacies. This is a sector where the ebbs and flows of demand intersect with global trade policies, making adaptability a key trait for survival. Recent years have seen a significant impact of geopolitical tensions on steel tariffs, leading to shifts in supply chain strategies that steel suppliers have had to navigate adeptly. For instance, the tariffs imposed on foreign steel have caused a ripple effect, enhancing the competitiveness of domestic suppliers while prompting international players to reassess their strategies. This intricate dance not only affects pricing but also influences where and how steel suppliers source raw materials.
Central to this is the role of technology which continually reshapes supply chain logistics. Automated systems and AI-enhanced analytics have revolutionized how raw materials are tracked, managed, and delivered to manufacturing plants. Efficiency has been the name of the game, and companies are investing heavily in supply chain tech to ensure a seamless flow from ore extraction to final product delivery. State-of-the-art inventory management systems now allow suppliers to predict demand with unprecedented accuracy, reducing waste and optimizing resource allocation. As one industry expert noted, "Modern supply chains are no longer just a linear path from raw materials to market. They are dynamic ecosystems, optimized for speed and resilience, constantly reacting to changes with remarkable precision."
Moreover, sustainability has steadily become a pivotal factor influencing market strategies. With an increasing focus on reducing carbon footprints, many leading steel manufacturing companies have taken significant strides towards greener operations. Initiatives such as recycling and reusing scrap steel, reducing reliance on fossil fuels through electric arc furnaces, and innovating in eco-friendly production methods are some paths being explored. Such efforts are not only environmentally beneficial but also serve as a competitive differentiator amid growing consumer awareness about sustainability issues.
In tandem with these developments, the supply chain's resilience has been put to test by disruptive events, ranging from pandemics to natural disasters. The COVID-19 pandemic illustrated vulnerabilities when global shutdowns led to a slowdown in production and delayed shipments, emphasizing the need for robust contingency planning and supply chain diversification. As the spotlight turns to ways of mitigating such risks, there is a greater push towards restructuring supply chains to enhance flexibility and reduce reliance on single suppliers or regions. In response, many US steel manufacturers are developing decentralized supply networks and diversifying sourcing to mitigate potential future disruptions.
Amidst these evolving dynamics, the use of strategic partnerships has become an essential part of the playbook for maintaining a competitive edge. Collaborations, especially with tech-driven young startups, are providing traditional steel giants with the agility and innovation required to stay ahead. By fostering relationships that help integrate new technologies and streamline supply chain processes, steel production leaders are securing their role as not just producers, but as pivotal components of the industry’s forward march into the future.
Technological Innovations in Steel Manufacturing
The steel industry has consistently been a fertile ground for innovation, driving efficiency and quality to meet rising global demands. Over recent years, technological advancements have reshaped how steel is manufactured, right from the extraction of raw materials to the creation of high-grade final products. Automation has played a significant role here, streamlining processes that once relied heavily on manual labor. Robotics and computer-aided design (CAD) now dominate production floors, ensuring precision and consistency in output.
A breakthrough that has gained prominence is the integration of artificial intelligence (AI) in monitoring and optimizing production. AI systems give steel plants the ability to analyze vast amounts of data in real-time, leading to smarter decision-making regarding resource allocation and energy usage. This ushers in cost-saving opportunities and a smaller carbon footprint – a critical consideration as industries worldwide strive for sustainability. According to a study by McKinsey, AI has the potential to increase productivity in the steel industry by as much as 30% over the next decade.
Another remarkable innovation is the development of electric arc furnaces (EAF), which are rapidly replacing traditional blast furnaces. These EAFs allow for the melting of scrap steel using electricity, significantly cutting down on the requirement for fresh iron ore and reducing overall greenhouse gas emissions. This not only helps fulfill environmental compliance but also enhances recycling efforts, turning waste into valuable resources. Moreover, advanced metallurgical techniques such as the ongoing research in nanotechnology promise to revolutionize the creation of stronger, yet lighter, steel alloys. These can be instrumental in fields such as automotive manufacturing, where weight reduction plays a crucial role in improving fuel efficiency.
"Technology is changing the face of steel manufacturing. Our commitment to innovation helps us meet the evolving needs of our customers and the environment," said John Ferriola, former CEO of Nucor Corporation, a leader in steel manufacturing. This sentiment is echoed across the industry, where investments in research and development continue to climb.
Additionally, the Internet of Things (IoT) has facilitated enhanced connectivity among machines and systems within manufacturing plants. This connectivity allows for predictive maintenance, where sensors track the working condition of machinery, foretelling failures before they arise and minimizing downtime. Through IoT, companies can access comprehensive insights into their production line, adjusting operations to optimize efficiency and product quality. Innovations like 3D printing are also making waves, proving to be a valuable tool in creating prototypes and small-batch production of customized steel components.
These advancements signify not just a technological evolution but a paradigm shift in how the steel industry aligns itself with modern industrial trends and environmental responsibilities. As this transformation unfolds, the role of technology in shaping THE future of steel production appears to be both pivotal and promising, offering solutions that balance industry growth with ecological sustainability.
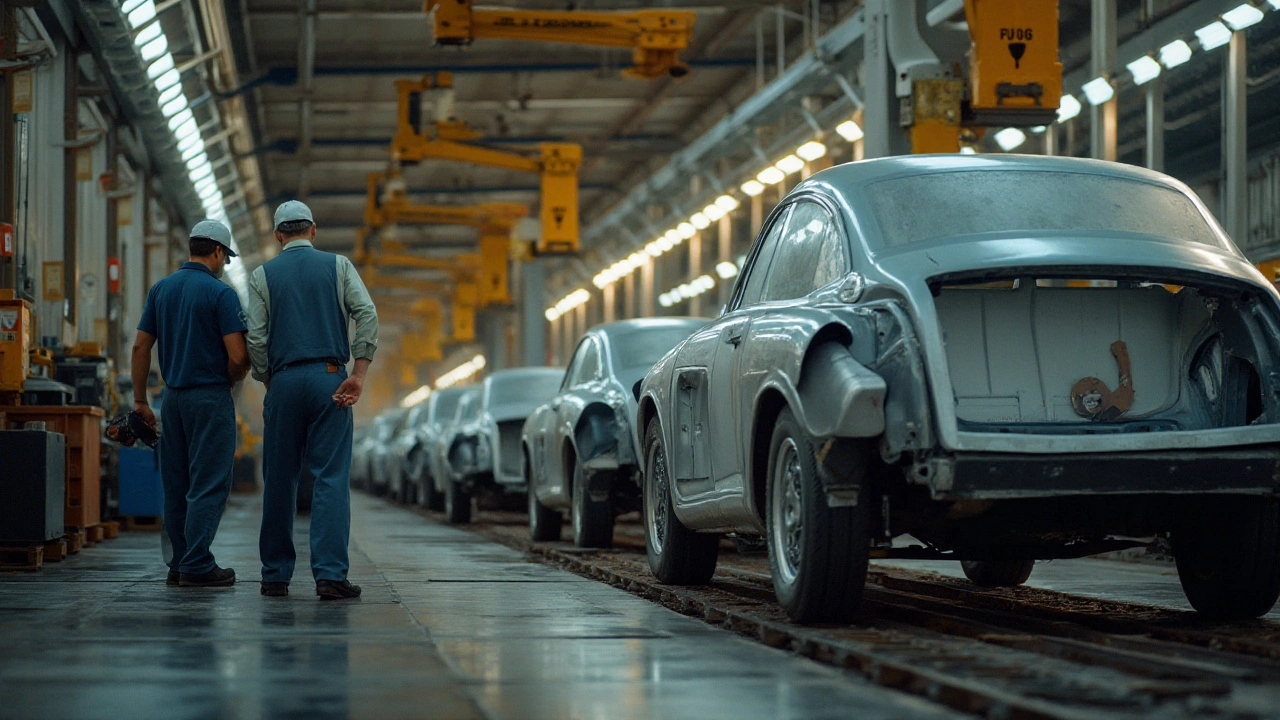
Future Outlook for the Steel Industry
The future of the steel industry in the United States is poised on the edge of significant transformation, driven by technological advancements, evolving market demands, and environmental considerations. As the global drive towards sustainability intensifies, the industry is being pushed to innovate and adapt. The use of electric arc furnaces (EAFs), which primarily recycle scrap steel instead of relying on newly mined iron ore, is becoming more popular. This technology not only reduces carbon emissions but also aligns with the rising trend towards a circular economy — a system that minimizes waste by reusing materials repeatedly.
Moreover, industries are increasingly looking at AI and advanced automation to improve production efficiency and reduce costs. A report by the International Energy Agency highlighted that "deploying smart manufacturing technologies could enhance production while at the same time cutting energy consumption by up to 15%." Companies investing in these technologies are likely to experience unique competitive advantages, paving the way for more sustainable production methods.
Government policies play a crucial role in this evolving landscape. Incentives for green manufacturing and stricter environmental regulations are expected to steer the industry further toward eco-friendly practices. This shift is not just a local phenomenon; global integration means that US steel producers must align with international standards to maintain their competitiveness on the world stage. In terms of market growth, there is optimism. The demand for steel is anticipated to increase, driven by sectors such as construction, renewable energy infrastructure, and transportation. In particular, the production of automobiles and electric vehicles, which rely heavily on lightweight, high-strength steels, is expected to grow significantly, prompting a surge in steel demand.
The pressure to innovate has also led to more significant research in developing new steel alloys and materials that can offer superior strength and durability while being lighter and more versatile. These new materials will likely find applications from aerospace to household appliances, expanding the realms of possibilities for what steel can achieve. Moving forward, the industry must also tackle the challenges of supply chain volatility and ensure reliable access to raw materials. As geopolitical tensions and global disruptions have shown, having robust logistical strategies will be crucial for companies looking to secure continuous operations.
Amid all these dynamics, leadership in the steel industry remains about balancing tradition and modernity. Companies that effectively harness new technologies, adopt sustainable practices, and agilely adapt to market changes will not only survive but thrive in the global arena. Their success will be measured not just by output but by how they respond to this new era of industrial evolution.