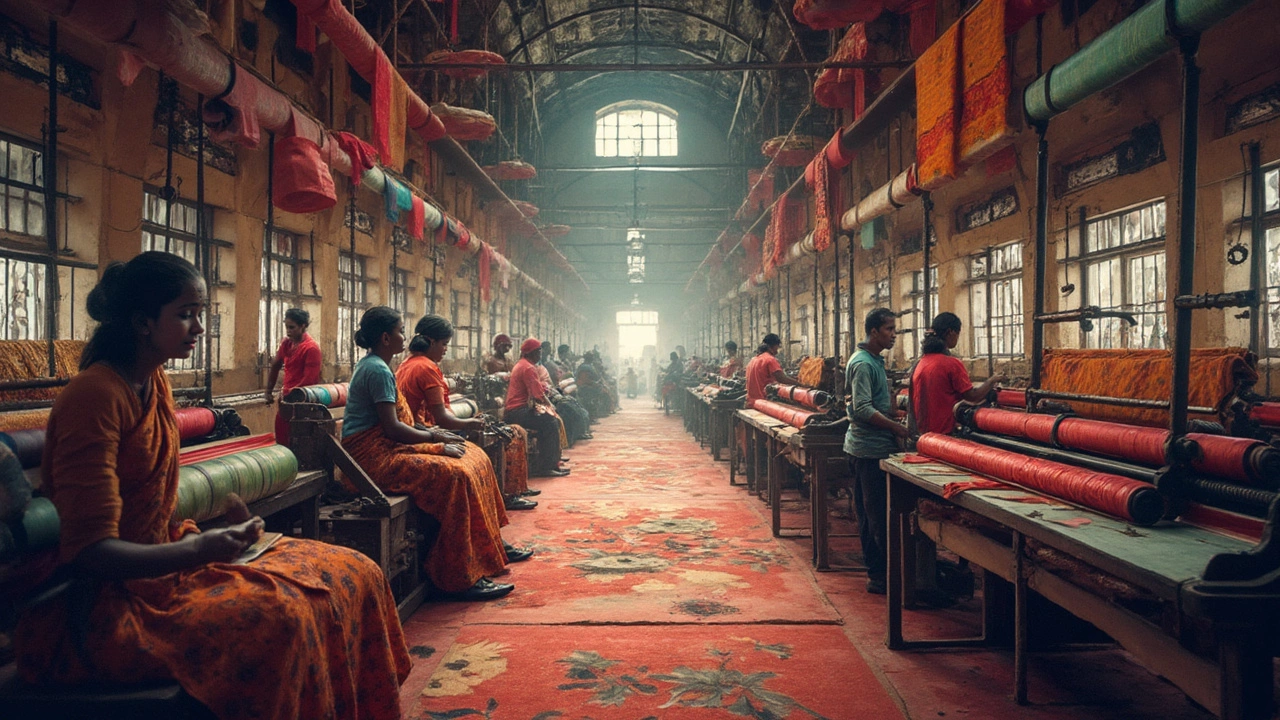
Ever thought about diving into the textile industry in India? It's a promising field but needs a clear understanding of the costs involved up front. First things first, there's land to think about. Depending on where you set up, prices can vary widely. Urban areas might be more accessible but come with a heftier price tag, while rural spots can be cheaper but might mean higher transport expenses.
Next up, equipment and machinery can be pretty pricey, accounting for a big chunk of the initial investment. Think about weaving machines, spinning tools, and knitting gadgets, just to name a few. Then there's staffing. India has a large pool of skilled workers, but training them for your specific needs is crucial and comes with its costs.
Operational expenses are another thing to consider. Electricity, water, and maintenance can add up, so planning for ongoing costs is key. To keep things afloat, it's smart to look into government incentives. Many programs offer financial assistance to textile startups in India, so be sure to do your research and see what's out there.
- Initial Setup Costs
- Essential Equipment and Machinery
- Staffing and Training
- Operational Expenses
- Tips for Cost Efficiency
Initial Setup Costs
Getting a textile factory up and running in India starts with some hefty initial investments. The first big factor? Land. Depending on where you plant your roots, the cost can swing drastically. Urban areas like Mumbai or Delhi can hit your wallet hard but place you nearer to major markets. Conversely, rural areas are more cost-effective for textile factory India setups, though you might need to shell out more for transportation infrastructure.
Land Acquisition
To figure out your expense here, consider how big you want to go. Are you looking at a few acres or something more expansive for serious production? Land cost can start at around ₹1,000 per square meter in more remote parts, but this can skyrocket in urban locales.
Construction
Next up is construction. Building your factory space could range from ₹1,500 to ₹3,000 per square foot. This covers the basic structure but remember to budget extra for specialized layouts or eco-friendly certifications, which are increasingly popular.
Machinery and Equipment
You can't skip on weaving and spinning gear. These essentials form the backbone of your textile manufacturing and make up another significant chunk of your outlays. A medium-sized setup might require anywhere from ₹2 crores to ₹5 crores for state-of-the-art equipment.
Permits and Licenses
Running any business in India means paperwork. Plan for permits, environmental clearances, and licenses. These can vary depending on your chosen area. Reserve roughly ₹10 lakh to ₹20 lakh for these initial bureaucratic hurdles.
An effective plan considers all these items to avoid nasty surprises down the road. Start by sketching a reasonable budget, and don't hesitate to tweak costs or rethink priorities. Keep this prep phase solid to set a strong base for your textile business journey.
Essential Equipment and Machinery
When setting up a textile factory in India, getting the right equipment is almost as vital as securing your building space. The type of machinery you'll need largely depends on the kind of textiles you're planning to produce—whether it's garments, home textiles, or industrial fabrics.
Key Machinery for Textile Production
First off, you'll need weaving machines. These are the backbone of many textile factories and come in various types like air-jet, rapier, and water-jet looms. Each type has its perks, with air-jet looms being super fast but needing more maintenance.
Then there are spinning machines. This equipment spins fibers into yarn and is crucial if you're dealing with the raw fibers. Many factories go for ring spinning machines due to their reliability and the quality of yarn they produce.
Knitting machines are a must-have if you're thinking of making knitted fabrics. These machines can be flat-bed or circular, each serving different types of knitwear. Choose based on your product range.
Additional Tools and Tips
Don't forget dyeing and printing machines if you plan to offer custom designs. These machines allow for flexibility in fabric designs—a big hit in today's custom-focused market.
Need to keep costs down? Look into second-hand machinery. Though they might require a bit more maintenance, refurbished machines can cut your initial equipment budget significantly while still giving you the output you need.
Keep in mind, whatever equipment you settle on, regular maintenance is key to ensuring longevity and keeping those lines running smoothly.
Machine Type | Estimated Cost (INR) |
---|---|
Weaving Machine (Air-jet) | 50 lakh |
Spinning Machine (Ring) | 60 lakh |
Knitting Machine (Circular) | 70 lakh |
By smartly selecting and maintaining your machinery, you set up a foundation for a resilient and profitable textile manufacturing venture.
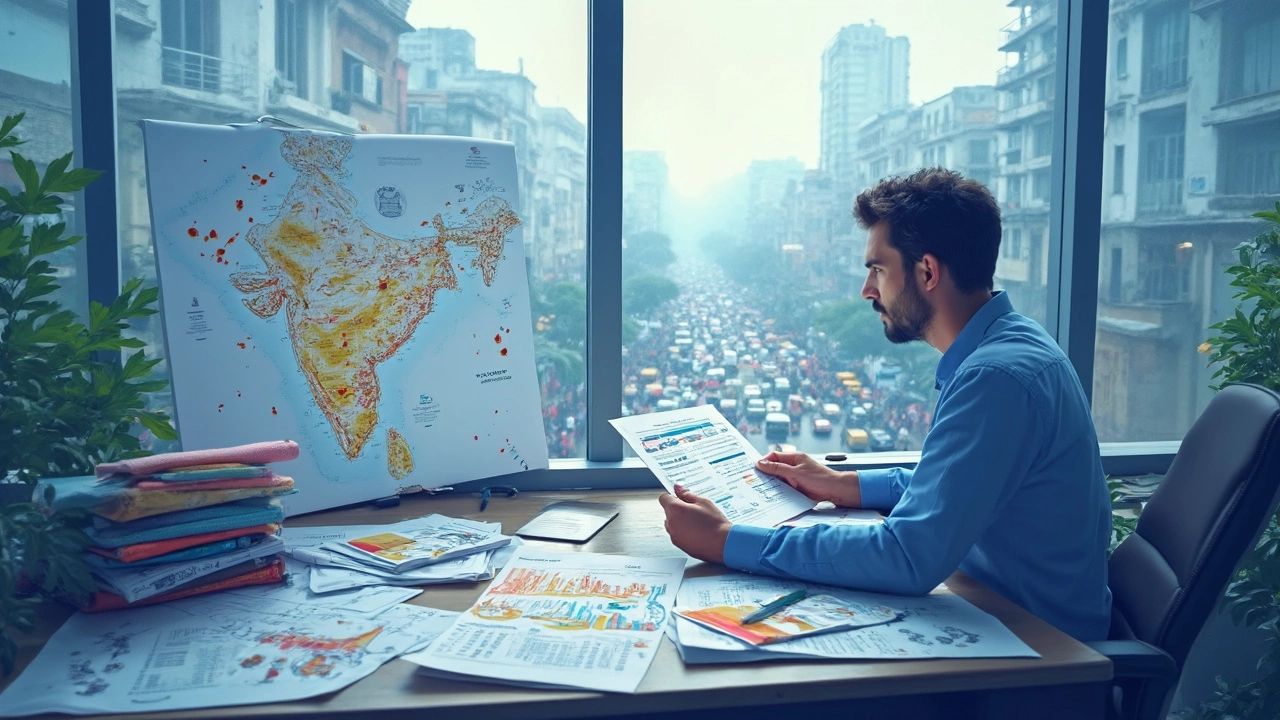
Staffing and Training
Setting up a textile factory in India isn't just about buying machinery and securing a location. The backbone of your operation will largely depend on the people you hire. From skilled operators who know their way around the latest weaving machines to managers who can ensure smooth day-to-day operations, finding the right team is crucial.
Finding the Right Talent
India's vast pool of skilled labor is one of your biggest advantages. There are countless training institutes churning out capable professionals ready to jump into the textile industry. Whether it's Tiruppur, a hotspot for knitwear, or Surat, known for its fabric and polyester production, tap into these local resources to find experienced candidates who can bring expertise to your factory.
Keep in mind that industry veterans suggest hiring a mix of experienced workers and fresh talent. The seasoned professionals can handle complex tasks, while the newcomers can be molded according to your specific needs.
Training Programs
No matter how skilled your workers are when they come on board, a thorough training program is key to ensure everyone is on the same page with your factory's practices. Training isn't a one-off event either; it's an ongoing process. Consider setting up a quarterly training schedule focusing on safety procedures, efficient production techniques, and quality control.
For those diving into textile manufacturing for the first time, collaborating with established textile training centers for specialized programs can be beneficial. These collaborations can bring fresh insights and push innovation within your operations.
Creating a Positive Work Environment
Your staff is more likely to stay long-term if they feel valued and secure. Ensure you adhere to labor laws, provide safe working conditions, and offer incentives like bonuses or healthcare. Happy employees are not only more productive but are also likely to contribute to a positive workplace culture.
According to recent data, companies that invest in employee development often see a 15% increase in productivity and employee retention. This is something to consider when you're budgeting for your staff.
In summary, while the markets and machines are important, never underestimate the power of a motivated, well-trained workforce in pushing your textile business to new heights. Prioritize finding and nurturing the right talent, and it'll pay off in the long run.
Operational Expenses
Running a textile factory in India isn't just about the setup. Daily operations can quickly rack up costs if you aren't careful, so it's important to get a handle on them right from the start.
Electricity and Water Costs
These are the backbone of your factory's operations. Machineries like spinning and weaving machines are power-hungry beasts. The electricity bill can be substantial, especially if you're operating in an area with high energy rates. Water, often overlooked, is vital too, especially if you're involved in dyeing processes.
Maintenance of Equipment
Staying on top of maintenance can save you a ton in the long run. Regular checks can prevent costly breakdowns. Form a maintenance schedule and stick to it, or set reminders if that's easier. Grabbing spare parts in advance can also avoid sudden expenses during emergency repairs.
Staff Salaries and Benefits
Your team is the heart of your operation. Salaries are a given, but don't forget about other expenses like insurance and potential bonuses. Indian labor laws require certain benefits, and it's good to be aware. Creating a motivated, well-compensated team often leads to better productivity.
Transportation Costs
Whether it's raw materials coming in or finished products going out, transportation eats up a good part of your budget. Fuel prices are always fluctuating, so it's wise to look into more efficient logistic solutions. Negotiate with carriers for better rates or even consider bulk shipping to cut costs.
Miscellaneous Costs
Think of security, office supplies, Internet services, and other administrative expenses. They may seem small individually but can grow over time. Budget for these upfront to avoid surprises later.
To help get a clearer picture, here’s a simple breakdown of what you might expect:
Expense | Estimated Monthly Cost (INR) |
---|---|
Electricity | 200,000 - 300,000 |
Water | 30,000 - 50,000 |
Maintenance | 50,000 - 100,000 |
Salaries | 500,000 - 1,000,000 |
Transportation | 100,000 - 200,000 |
Miscellaneous | 50,000 - 100,000 |
As you can see, operational expenses are a mixed bag of ongoing costs that need attention. Hopefully, this helps in giving you a clear view so you can plan effectively and keep your textile business running smoothly.
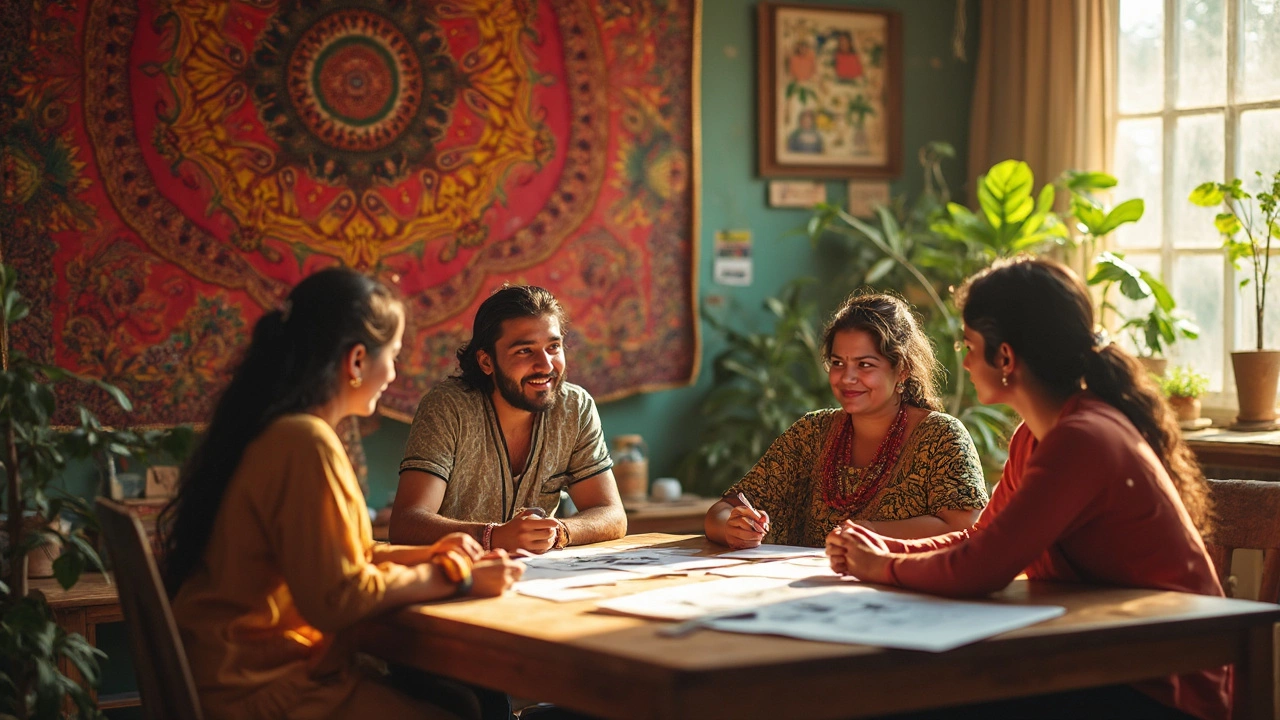
Tips for Cost Efficiency
Starting a textile factory in India isn't just about knowing the costs; it's about being smart with your spending. Here are some practical tips to help you keep a lid on expenses and make the most out of your investment.
Choose the Right Location
Location plays a big role in setting up costs. Urban areas might seem appealing, but don't overlook semi-urban or rural areas. Land is usually cheaper in these spots, plus you might qualify for government incentives aimed at boosting local employment.
Invest in Energy Efficiency
One way to save money in the long run is by investing in energy-efficient machinery right from the start. While initial costs might seem high, you'll see significant savings on energy bills over time. Many textile business cost calculators include these potential savings in their assessments.
Use Local Resources
India is rich in natural resources like cotton and jute. By sourcing materials locally, you can slash transportation costs and support the local community, which could further boost your business reputation.
Take Advantage of Technology
Don't shy away from technology. Automating certain processes can reduce labor costs and increase efficiency. Plus, software for inventory and process management can help you avoid waste and keep a tight rein on expenses.
Government Schemes and Subsidies
Check out the various government schemes available for new textile enterprises. These can drastically reduce costs. For example, the Technology Upgradation Fund Scheme (TUFS) offers subsidies for modernizing equipment.
Cost Component | Potential Savings |
---|---|
Energy Bills | Up to 30% with efficient machinery |
Material Transport | 20-25% by sourcing locally |
Every Rupee saved can be reinvested into growing your business. The key to maintaining cost efficiency isn't just about cutting costs, but about smart investments that pay off over time. Keep these tips handy and give your business the best chance at thriving in India's textile industry!