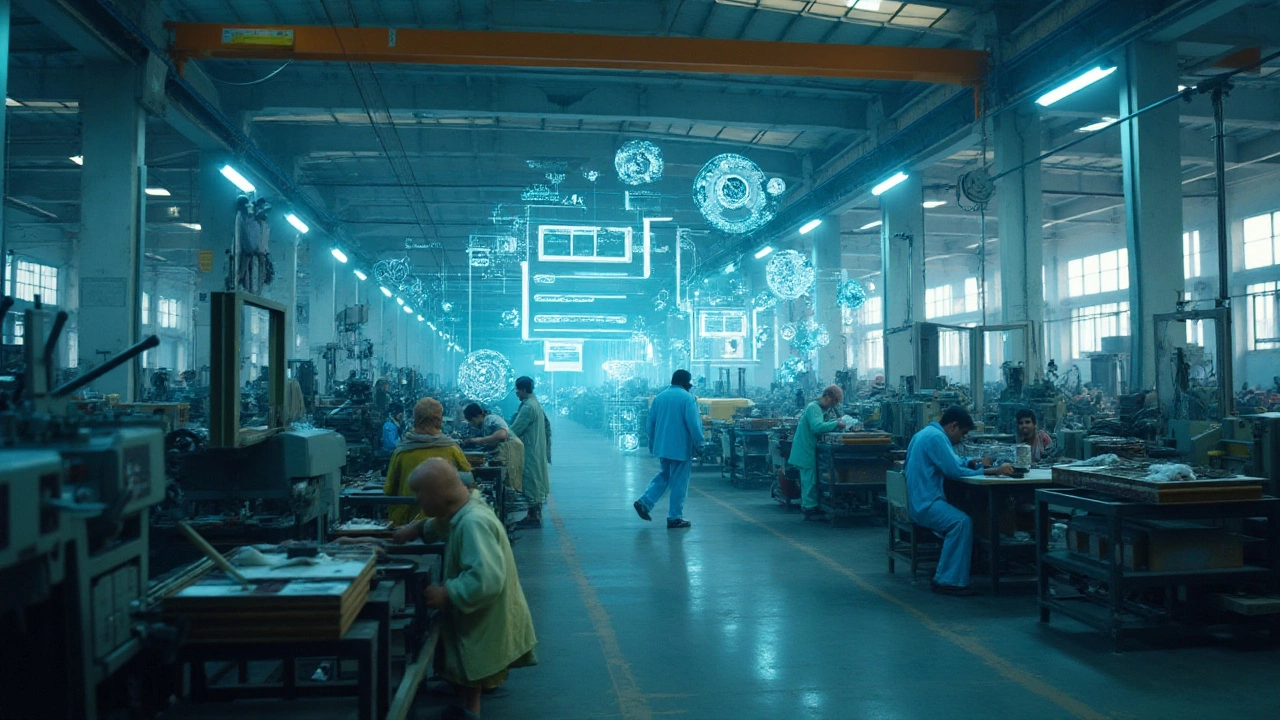
The world of manufacturing is rich with opportunity but also fraught with challenges. One of the most persistent challenges is waste. Whether it's wasted time, materials, or resources, waste can significantly drive up costs and dampen efficiency. For those venturing into this industry or seeking to innovate within it, understanding how to identify and reduce waste is crucial.
In today's manufacturing landscape, innovations are as much about cutting inefficiencies as they are about creating groundbreaking products. The practice of lean manufacturing offers a framework for recognizing and eliminating waste, leading to more streamlined production processes. But, what are the biggest culprits of waste, and how can they be turned into opportunities for innovation?
This exploration will navigate through various aspects of waste in manufacturing, shedding light on strategies and startups that are making significant strides towards a more efficient and sustainable future. If you're ready to delve deeper into the practicalities of reducing waste, you're in the right place.
- Understanding Waste in Manufacturing
- Types of Manufacturing Waste
- The Impact of Waste on Costs and the Environment
- Introduction to Lean Manufacturing
- Strategies to Minimize Waste
- Innovative Solutions and Startups Pioneering Change
Understanding Waste in Manufacturing
In the dynamic and fast-paced world of manufacturing, waste is an immense, yet often underappreciated, component. It is not just about physical remnants that pile up in landfills; waste encompasses much more in this industry. It spans from excessive production and waiting times to inefficient workflows and unused skills. Underpinning this notion is the reality that waste significantly elevates production costs, diminishing the potential profits and environmental sustainability of manufacturing operations. This presents a sizable challenge for manufacturers who are starting or retooling their operations.
Commonly referenced in business improvement strategies is the Japanese concept of 'muda,' which refers to any activity that doesn't add value to the customer. In other words, 'muda' is synonymous with manufacturing waste. Alongside this are the other two concepts known as 'mura' (unevenness) and 'muri' (overburden), which together frame the guiding principles for achieving streamlined operations in lean manufacturing practices. By identifying 'muda', businesses can transform waste into a catalyst for efficiency and growth. This is where the real challenge lies—not just eliminating waste, but understanding and leveraging it as an opportunity to enhance productivity and ingenuity.
Dennis P. Nobelius once remarked, "Waste is only what we choose to see." His words echo the truth that recognizing waste is the first step in addressing it.
There's also a structural component to waste. Consider how downtime in production lines can lead to prolonged delays and missed deadlines. This timing misalignment occurs in countless ways throughout a manufacturer's routine operations, from waiting around for raw materials to be delivered to inefficient use of equipment. Such inefficiencies create a ripple effect that balloons costs and stifles output. Whereas, adopting an efficient material flow can help counteract these issues, enabling just-in-time production that aligns with purchasing and scheduling strategies.
How can one begin to address these types of waste? Analyzing production data to pinpoint frequency and duration of downtime is critical. Many companies are now employing data analytics in their operational strategies as a significant first step in waste reduction. Utilizing smart technologies to gather and analyze this data can identify trends and uncover opportunities to optimize processes and resource allocation. For instance, predictive maintenance strategies can be used to minimize equipment failures, which are notoriously costly in terms of downtime and repair.
Ultimately, understanding the various types of waste involves as much about building a culture of continuous improvement as it does about technological adoption. Teams need to champion a mindset that embraces inquiry and accountability across all levels of the organization. It’s this intrinsic investigation into operational processes that leads to substantial advancements over time. The aim is both clear and ambitious: to create valuable products and services in a manner that is inherently mindful of resources and sustainability, thus meeting the demands of modern consumers as well as staying one step ahead of regulatory pressures.
Types of Manufacturing Waste
When it comes to identifying the biggest obstacles in manufacturing, waste ranks high on the list. To combat waste, you must first understand its many forms. One prominent type is excess inventory, which often ties up capital and takes up space. Goods unaccounted for due to overproduction or delays tend to stack up, leading to higher storage costs and even potential damage or obsolescence. It's common for businesses to fall into the inventory trap, thinking more stock automatically equals more security against sudden demand surges. In reality, this often results in a surefire path towards inefficiency.
Another significant waste is caused by inefficient transport. Moving products from one place to another, whether within a facility or between locations, demands energy and resources. Unnecessary movement does not add value but instead drives up costs and can even lead to damage or spoilage. Streamlining this aspect of manufacturing often requires a keen eye for logistics and strategically placed workstations to cut down on needless transit.
"Transportation itself becomes a form of inventory, carrying cost implications often overlooked," says Jim Womack, a founding member of the Lean Enterprise Institute.
But the waste does not stop there. Consider the time lost due to waiting. Machines breakdown, materials do not arrive as scheduled, and labor may be left waiting, idling productivity. Each minute of waiting represents not just time lost but money too. Addressing this requires a robust schedule management system, often employing principles from lean manufacturing to minimize downtime. This leads right into overprocessing, where more work is done than necessary. Overprocessing often stems from a lack of effective communication and incorrect use of machinery or labor, creating more product iterations than needed.
Then there's the human factor: excess motion, which deals with unnecessary physical movements by workers. Whether it's reaching too far or walking too much, reducing excess motion is vital in keeping employees more productive and less fatigued. Implementing ergonomic solutions and optimizing workspace layout can greatly alleviate this issue. Finally, we cannot ignore defects, arguably the most direct form of waste, which occurs when products do not meet quality standards, requiring rework or, worse, complete scrapping. Reducing defects often comes down to establishing a culture of quality and continuous improvement, where every step is analyzed to catch potential issues early on.
Here’s a simple breakdown of some of these waste types and their characteristics:
Type | Characteristic |
---|---|
Excess Inventory | High storage costs, risk of obsolescence |
Inefficient Transport | Unnecessary movement, damaged goods |
Waiting | Idle labor and machines |
Overprocessing | Extra work beyond requirements |
Excess Motion | Unnecessary worker movements |
Defects | Rework and product scrap |
Recognizing these types of waste in manufacturing processes is the first step towards eliminating them, enabling smoother operations and opening the door to new innovative startup ideas in the field. By addressing these wastes, companies not only cut costs but also boost efficiency and contribute to more sustainable manufacturing practices, showing that efficiency and environmental responsibility can indeed walk hand in hand.
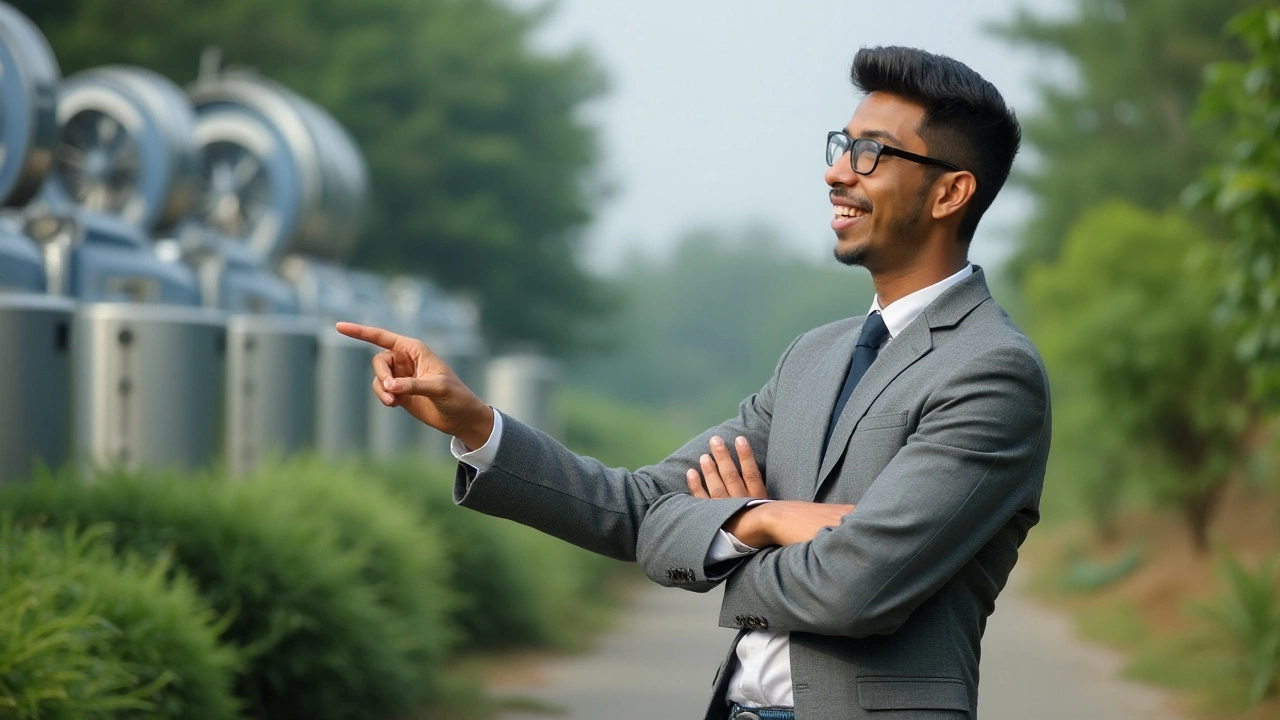
The Impact of Waste on Costs and the Environment
Waste in manufacturing isn't just about what ends up on the factory floor; it's a multifaceted issue that touches both the financial health of a company and the well-being of our planet. From defective products to excessive energy consumption, the ripple effects of waste are far-reaching. Financial costs soar, as inefficient processes demand more resources than necessary – a burden that can cripple smaller manufacturing startups trying to get off the ground. Consider this: for every defective item, there's the compound cost of materials, labor, and lost opportunities. Not to mention the added expense of managing waste, which can escalate without rigorous waste reduction strategies.
The environmental ramifications are equally pressing. When companies use resources inefficiently, they often overdraw from the planet's reserves, contributing to unsustainable resource depletion and pollution. Landfills swell with industrial waste, and the toxic byproducts of wasteful practices can leech into the soil and waterways, threatening ecosystems. According to a report by the EPA, American manufacturing produces approximately 7.6 billion tons of waste annually. This massive figure highlights the urgent need for improvements and the role that innovative, modern manufacturing methods can play in alleviating this crisis.
"The real enemy of production efficiency is waste. But, in addressing it, we are also fighting for a healthier planet," says John Smith, a leading expert in production efficiency at MIT.
Aside from the obvious financial and environmental costs, manufacturing waste can damage a company's reputation, affecting consumer trust and brand loyalty. Today’s consumers are more informed and environmentally conscious, often scrutinizing a company's environmental footprint before deciding where to spend their money. Manufacturing startups, in particular, must tread carefully and demonstrate commitment to sustainability if they hope to capture the modern consumer's heart. Ill-managed waste can also complicate regulatory issues, as governments worldwide tighten regulations on emissions and waste management. This evolving legal landscape means that the financial implications of waste extend beyond just internal costs, potentially leading to fines or sanctions for non-compliance. Addressing these issues requires a fundamental shift towards embracing principles of lean manufacturing, reducing excess, and enhancing resource efficiency, not only to safeguard the bottom line but also to secure a sustainable future for the planet.
Introduction to Lean Manufacturing
Lean manufacturing is a powerful methodology that originated in the Japanese automobile industry, with Toyota being one of its earliest pioneers. At its core, lean manufacturing is about maximizing value by minimizing waste. The idea is simple: identify what's valuable to the customer and cut out everything else. This lean approach has become a guiding principle across various industries worldwide, influencing not just production lines but entire supply chains. Central to this practice is the relentless pursuit of eliminating non-value activities—commonly known as the 'wastes' of manufacturing. By focusing intensely on these aspects, companies can improve their competitiveness by reducing costs, speeding up production times, and enhancing product quality.
Lean manufacturing identifies seven types of waste: transport, inventory, motion, waiting, overproduction, overprocessing, and defects. Each of these wastes can significantly impact a company's efficiency. Consider inventory waste, for example, which involves excessive stock that holds up capital and space. Applying lean principles, businesses aim to streamline inventory to only what is needed for the immediate future. Similarly, overproduction, which means producing more than needed and often before demand warrants, can trap resources in unsold stock, adding to waste.
To better institutionalize lean practices, businesses often adopt techniques such as Kaizen, which translates to 'continuous improvement.' Kaizen is not just a method; it's a mindset encouraging all employees, from factory floor workers to top executives, to continuously seek ways of improving processes. According to lean manufacturing expert James P. Womack, "Lean thinking does precisely what modern companies need: it integrates the flexibility of automation with the personal involvement of human intelligence." Effective lean manufacturing goes beyond individual components, influencing organizational culture by empowering teams to systematically root out inefficiencies.
Reflecting on lean manufacturing's impact, consider that implementing these methods can lead to remarkable fiscal benefits. For instance, companies have reported achieving up to a 50% reduction in lead times and a 30% increase in production efficiency. To visualize this, a table might show a comparison of production metrics before and after adopting lean methods, with marked improvements across the board. By constantly refining processes and leveraging team insights, organizations can foster an environment of proactive problem-solving and innovation.
"Lean manufacturing is not a cost-reduction program. It's a growth strategy that aligns operations with the changing needs of customers," emphasizes Dr. Jeffrey Liker, author of 'The Toyota Way.' This quote encapsulates the transformative potential of lean principles, which extend beyond simply cutting down waste to influencing how companies grow and thrive in evolving market landscapes.
As startups tackle the multifaceted challenges of the manufacturing industry, understanding and applying lean manufacturing principles can become a competitive advantage. They can innovate not just by creating new products but by cultivating more efficient, adaptable, and responsive production processes. For entrepreneurs aiming to create a business legacy, lean manufacturing offers a distinguished pathway towards operational excellence and sustainable growth.
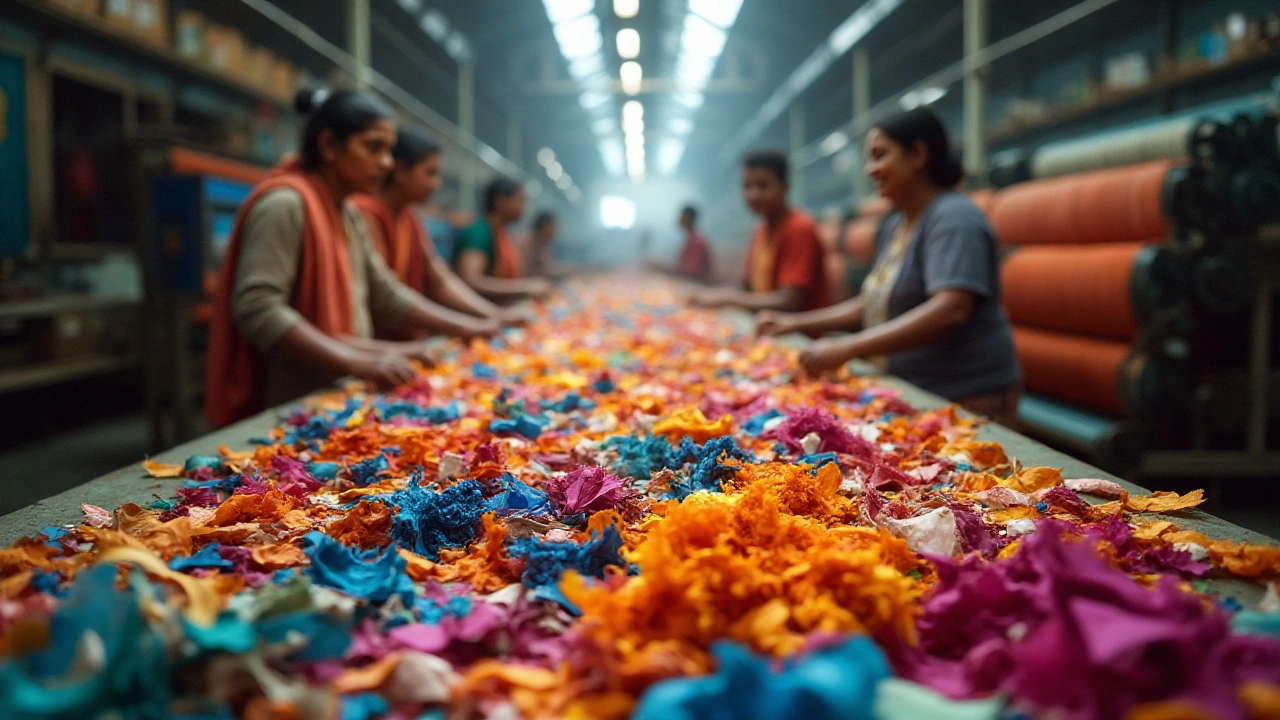
Strategies to Minimize Waste
In the fast-paced world of manufacturing, reducing waste is not just a cost-saving strategy but a philosophy that can drive transformation across industries. Embracing techniques to minimize waste requires a multi-faceted approach, often starting with data-driven decision-making. One of the basic steps is implementing a thorough audit to pinpoint sources of manufacturing waste. Identifying and understanding waste types such as overproduction, waiting times, unnecessary transport, overprocessing, and excess inventory, according to lean manufacturing principles, sets the stage for targeted action.
An effective strategy involves incorporating continuous improvement methodologies such as Kaizen, which encourages incremental and ongoing refinements within production processes. By fostering a culture where employees at all levels are empowered to suggest and implement improvements, companies can significantly reduce waste and enhance production efficiency. Technological advances also play a pivotal role, where smart manufacturing systems and IoT devices provide real-time monitoring and data analysis capabilities. This tech integration allows for predictive maintenance, potentially reducing downtime that contributes to waste.
Moreover, innovative supply chain management plays a crucial part in minimizing waste, especially in the context of unsold inventory or overordered materials. Techniques like Just-in-Time (JIT) inventory systems ensure materials and products are produced or acquired only as needed, drastically reducing the probability of waste due to excess stock. This strategy not only reduces storage costs but also mitigates the risk of obsolescence. Embracing sustainable practices goes hand-in-hand with waste minimization, where recycling and reusing materials can significantly cut down on raw material costs and environmental impact.
Utilizing Technology and Data
Today's digital tools provide an unprecedented opportunity to tackle manufacturing inefficiencies. Utilizing advanced analytics can identify inefficient processes that were previously invisible. Machine learning algorithms can optimize production schedules, forecasting demands while minimizing overproduction and accommodating real-time changes. According to a recent study in the International Journal of Production Economics, companies leveraging data analytics have reported a reduction in waste of up to 20%. This data-driven approach enables a finer granular targeting of cost-intensive bottlenecks over traditional methods.
A 2019 report by the World Economic Forum concluded that factories implementing AI-driven waste reduction platforms could see productivity increases of 10% to 30% by simply optimizing operational parameters and reducing unnecessary waste factors.
Investing in workforce training is another essential strategy. With advanced tools and machines, operators need to be appropriately trained not only to use new technologies but also to understand lean concepts deeply. Training programs that include real-case scenarios and problem-solving exercises foster more robust engagement among the workforce, empowering them with the skills to identify waste and troubleshoot solutions effectively.
Collaborative Initiatives
Collaboration within and across different sectors of the manufacturing landscape holds immense potential. Aligning goals with suppliers, partners, and even competitors for joint waste reduction initiatives can lead to shared benefits. Companies have begun to form industry-wide consortia to share insights, success stories, and even failures, fostering a collaborative environment for best practice dissemination. Some initiatives include developing shared platforms where waste materials from one company can serve as raw inputs for another, exemplifying a circular economy's essence in practice.
The implementation of these strategies shows that minimizing waste goes beyond merely reducing costs. It encompasses systemic changes that benefit the environment and society. An innovative approach to waste reduction opens the doors to new startup ideas in manufacturing, presenting exciting opportunities for entrepreneurs to develop novel solutions that target each stage of the waste cycle with precision and creativity.
Innovative Solutions and Startups Pioneering Change
In the dynamic world of manufacturing, new companies are constantly emerging, armed with the ambition to tackle the eternal problem of waste. These pioneers are not merely tweaking existing processes, but are reimagining them, transforming manufacturing waste into useful byproducts or even fully viable products in their own right. A leader in this space is the startup Renewlogy, which has developed a technology to convert plastic waste into fuel. This ingenious technology not only addresses the environmental crisis posed by discarded plastics but also alleviates the cost concerns associated with disposing of these materials. It's a solution that turns a liability into a valuable asset.
An essential part of this innovation trend is the application of digital technologies to traditional production lines. For instance, the use of Internet of Things (IoT) sensors allows manufacturers to monitor their equipment's health and performance in real-time, predicting failures before they occur. This predictive maintenance is a game-changer, as it significantly reduces the costly downtime of machinery and prevents the premature disposal of perfectly usable equipment. Companies like Uptake and C3.ai are at the forefront, offering platforms that harness AI to provide actionable insights from the collected data.
Another exciting arena is the development of eco-friendly materials by startups like Algix, which produces bioplastic materials from algae. This innovation not only addresses the manufacturing waste challenge but also contributes to carbon reduction, as algae naturally absorb CO2. Moreover, these materials are biodegradable, offering an attractive alternative to traditional plastics. Algix's technology demonstrates that waste isn't merely a problem to dispose of but an opportunity to create better, more sustainable manufacturing inputs.
3D printing has also opened up a world of opportunities for minimizing waste. By its nature, 3D printing generates significantly less waste compared to traditional subtractive manufacturing methods. Startups such as Carbon3D are pushing the boundaries by developing faster and more efficient 3D printers that use less material and allow for greater design flexibility. This technology empowers manufacturers to iterate rapidly, reducing material waste from discarded prototypes and excess inventory.
"Innovation isn't about creating something new; it's about redefining how we use what already exists," says Michael Dell, reflecting the philosophy that many of these startups embody.
Blockchain technology is making waves, especially in ensuring transparency and accountability within supply chains. This digital ledger system can track and authenticate every input and process stage, significantly reducing the production inefficiency resulting from errors or mismanagement. Startups like Provenance and Everledger are pioneering these applications, offering solutions that could drastically enhance efficiency and reduce waste across entire supply chains.
The path forward for minimizing waste in manufacturing is paved with potential thanks to these innovative solutions. It's inspiring to see how startups are leveraging technology not only to address waste but to turn it into a springboard for new business models and sustainable practices. As awareness and technology continue to grow, the future of manufacturing startups holds promise for a more efficient, cleaner industry, one where waste is no longer an unavoidable byproduct but a catalyst for creativity and change.